Following a recent meeting at Safety Pass Alliance with some key members of the Food Industry and experienced trainers. We are pleased to announce that the new Food and Drink Sector Package V5 is in development. Updates will be announced in the new year.
Author Archives: Shirley Lovegrove
Roofing Firm fined
Roofing firm fined after worker injured by machinery
- Date:
- 26 November 2015
Roofing and insulation firm IKO Plc has been prosecuted after a worker suffered arm injuries while at work.
Graeme Myers, 48, from Belper, who was self-employed, was lubricating a chain on an auto-plant machine at Prospect Quarry in Matlock on 2 July 2014 when he reached over a fence at the end of the machine. The machine was still running and the pusher block used to transport empty trays moved forward striking his arm.
Mr Myers required immediate surgery to close the wound to his arm and he has been left with muscle loss and nerve damage. He was unable to work for three months.
Chesterfield Magistrates Court heard that the fence height should have been enough to prevent access to the pusher block and other dangerous parts of the machine. However when IKO Plc moved the machine from its previous location it failed to identify the change in floor level which reduced the height of the guard, allowing access to the dangerous parts.
IKO Plc of Appley Bridge, Wigan pleaded guilty to breaching Regulation 11 (1) of The Provision and Use of Work Equipment Regulations 1998 and were fined £10,000 and ordered to pay costs of £2331.21 and a victim surcharge of £120.
Speaking after the hearing, Health and Safety Executive Inspector Lyn Spooner said: “This was a very simple case where IKO Plc had overlooked the conditions of its new site in its risk assessment and as a result failed to identify the reduced height of the fence guard, allowing access to dangerous parts of the machine. It was an obvious risk, and as a result one their workers was seriously injured.
“Companies must prevent access to dangerous parts of machinery in order to prevent serious injury and in cases like this there are often simple measures that could and should have been taken to prevent the accident occurring ”
Notes to Editors:
- The Health and Safety Executive (HSE) is Britain’s national regulator for workplace health and safety. It aims to reduce work-related death, injury and ill health. It does so through research, information and advice, promoting training; new or revised regulations and codes of practice, and working with local authority partners by inspection, investigation and enforcement. www.hse.gov.uk[1]
- More about the legislation referred to in this case can be found at: www.legislation.gov.uk/
[2]
- HSE news releases are available at http://press.hse.gov.uk
Agency Worker fatal fall
Teesside firm fined after worker’s fatal fall
- Date:
- 23 November 2015
A north east port has been fined £400,000 following the death of an agency worker who fell eight metres onto the steel deck of ship’s hold at Hartlepool Dock
Robert Harrison, 59, from Middlesbrough, was one of six men who were loading 12m long steel pipes into the hold of a vessel at PD Teesport Ltd, at Hartlepool Dock, in Cleveland Road, Hartlepool, when the incident happened on 9 September 2012.
The incident was investigated by the Health and Safety Executive (HSE), which prosecuted PD Teesport Ltd for serious safety failings.
Teesside Crown Court heard how Mr Harrison, an agency worker, and his colleagues were standing on top of the stack of pipes. The stack increased in height as more pipes were loaded in to the hold using a dockside crane to lift and lower them into position in the ship’s hold.
Mr Harrison fell from the exposed edge of the stack of pipes, landing onto the steel deck of the hold eight metres below. He later died in hospital as a result of his injuries.
The HSE investigation found that there were exposed edges at either end of the pipes, ie, between the ends of the pipes and the bulkhead of the vessel and also the open edge, and the company did not provide appropriate measures to prevent or minimise the risks from falls.
PD Teesport Limited, of Queen’s Square, Middlesbrough, was fined £400,000 and ordered to pay £107,684.40 costs after pleading guilty to breaching Section 3(1) of the Health and Safety at Work etc Act 1974.
After the hearing, HSE inspector Cain Mitchell said: “Robert Harrison, a father of three, lost his life needlessly because of the failure by PD Teesport Ltd to put effective safety measures in place.
“This was a tragedy that could have very easily been prevented. The company should have properly assessed the risks and ensured appropriate measures were in place to reduce the risks of falling. The risk of a fall from an 8 metre stack of pipes was obvious. These precautions could have included the use of soft landing systems such as an air bag or cushion, which would have ensured no significant injury could result from a fall.”
More information about working at height safely can be found on the HSE website at: http://www.hse.gov.uk/work-at-height/index.htm[2]
Notes to Editors:
- The Health and Safety Executive (HSE) is Britain’s national regulator for workplace health and safety. It aims to reduce work-related death, injury and ill health. It does so through research, information and advice, promoting training; new or revised regulations and codes of practice, and working with local authority partners by inspection, investigation and enforcement. hse.gov.uk[3]
- Section 3(1) of the Health and Safety at Work etc Act 1974 states: “It shall be the duty of every employer to conduct his undertaking in such a way as to ensure, so far as is reasonably practicable, that persons not in his employment who may be affected thereby are not thereby exposed to risks to their health or safety.”
- HSE news releases are available at http://press.hse.gov.uk/
Fire Extinguisher Safety Alert
Norfolk Range’ large wheeled dry powder fire extinguishers manufactured before 2009 by UK Fire International Ltd
Health and Safety Executive – Safety Alert | |
---|---|
Department Name: | Hazardous Installations Division, CEMHD, unit 1C |
Bulletin No: | HID 1-2015 |
Issue Date: | 12 August 2015 |
Target Audience: | All premises where large dry powder fire extinguishers are likely to be used for example: chemical industry, offshore industry, merchant shipping, nuclear industry, manufacturing, mining, warehousing, engineering, metals and minerals processing and production. |
Key Issues: | ‘Norfolk Range’ large dry powder fire extinguishers, manufactured before 2009, may be affected by moisture ingress at a threaded joint at the base of the unit, rendering the unit inoperable. The problem may not be identified during routine service inspections.
|
Introduction:
At a recent fire on a chemical plant, three wheeled dry powder fire extinguishers, containing 45kg of Monnex dry powder, failed to discharge when activated. This safety alert relates to dry powder units manufactured between 1970 and 2009. An identifying feature of these units is that the discharge hose is coupled at the base of the unit via a threaded metal elbow joint.
Photograph 1 shows the type of unit covered by this alert.
If you are unsure if your units are affected by this safety alert, consult Britannia Fire Ltd.
Background:
The units operate by opening a CO2 cylinder attached to the body of the extinguisher. The main body of the extinguisher holds the dry powder. The powder is discharged through a hose and is pushed out by the pressure of CO2. The units in scope of this alert have a discharge hose attached to the base of the body of the extinguisher by a piped metal elbow.
HSE examined three of the above units that failed to operate. Each had rust visible on the inside of the elbow joints. The extinguishers had been kept outdoors under plastic covers and had been serviced every six months. The service engineers had noted the rust but it was not thought to affect the operation of the units.
The flexible discharge hose is normally removed during servicing however the elbow joint is not usually disturbed. It is believed that water ingress at this joint resulted in caking of the dry powder within the elbow joint. The caked powder may fall back from the discharge tube into the body of the extinguisher and so not seen during basic servicing. Upon activation of the extinguisher, the caked powder can block the discharge hose and render the unit inoperable.
Photograph 2 shows the rusted joint and caked powder from a unit that failed to operate. When the flexible discharge hose was removed the blockage was not visible. It was only identified when the elbow was removed from the body of the extinguisher.
The revised design of ‘Norfolk Range’ extinguishers produced by Britannia Fire Ltd is not affected by this problem. The design of the later versions features hoses mounted to the top of the unit, as shown in photograph 3.
Action required:
- You should inspect any ‘Norfolk Range’ wheeled dry powder fire extinguishers and confirm if you have a unit with a discharge tube connected to the bottom of the unit.
- If the extinguisher has been left exposed to adverse conditions since its last extended service, the condition of the elbow joint should be examined by a competent fire extinguisher service engineer.
- Service engineers should closely examine, and if necessary, remove the elbow to confirm if there is evidence of water ingress to the discharge tube. If there is any doubt about moisture affecting the powder in the discharge tube, consider subjecting the extinguisher to an extended service including full replacement of the dry powder.
- Service engineers should advise clients to consider storing this type of extinguisher in a location where it is protected from rain or very damp conditions.
Relevant legal documents:
- Provision and Use of Work Equipment Regulations 1998 regulation 5
- Regulatory Reform (Fire Safety) Order 2005, Article 17
- Fire Safety (Scotland) Regulations 2006, as amended, regulation 16
- The Offshore Installations (Prevention Of Fire And Explosion, Emergency Response) regulations 1995 PFEER regulation 19
References:
- Britannia Fire Ltd – Procedure for servicing and recharging Norfolk Range transportable fire extinguishers
[4]
- BS 5306-3:2009 Fire extinguishing installations and equipment on premises. Commissioning and maintenance of portable fire extinguishers. Code of practice
Further information:
- Britannia Fire Ltd, Ashwellthorpe Ind Estate, Ashwellthorpe, Norwich, Norfolk, NR16 1ER, tel: 01508 488416
website: http://www.britannia-fire.co.uk/[5]
- Health and Safety Executive online advice form[6].
General note:
Please pass this information to a colleague who may have this Product/ Equipment or operate this type of system/process.
Saw mill fined
Saw mill fined after employee suffers severe hand injuries
- Date:
- 7 October 2015
A saw mill in Kettering was fined after an employee suffered a serious injury to his left hand.
The agency worker, was working at Brigstock saw mill on 14 August 2014 when his hand was drawn into the rotating blade of an inadequately guarded large band saw.
Northampton Magistrates’ Court heard on Tuesday 6 October 2015, that the agency worker had been working on the saw with another employee and he had been levering the material being fed to the saw using a crow bar when he slipped and his left hand was drawn into the blade. His ring finger was badly damaged and later required plastic surgery.
An investigation by the HSE found the company had failed to ensure that effective measures were taken to prevent access to the dangerous parts of the saw.
Following the accident, Brigstock Saw Mill has installed a protective wooden box to ensure that operators are not able to stand within close distance to the blade of the saw.
Midlands Renewable Fuels LLP (Brigstock saw mill), was fined £5,000 with costs of £876.50 and a £175 victim surcharge, after pleading guilty to breaching Regulation 11 of the Provision and Use of Work Equipment Regulations 1999.
After the hearing, HSE inspector Jenna McDade, said:
“Had the company taken suitable measures to ensure workers did not come into contact with the rotating blade, this incident would have been easily prevented. Had the saw been properly guarded, the agency worker would not have been injured.”
Notes to Editors:
- The Health and Safety Executive (HSE) is Britain’s national regulator for workplace health and safety. It aims to reduce work-related death, injury and ill health. It does so through research, information and advice, promoting training; new or revised regulations and codes of practice, and working with local authority partners by inspection, investigation and enforcement. www.hse.gov.uk[2]
- More about the legislation referred to in this case can be found at: www.legislation.gov.uk/
[3]
- HSE news releases are available at http://press.hse.gov.uk
Laundry firm prosecuted
Laundry firm prosecuted after worker suffers third degree burns
- Date:
- 11 September 2015
A Stockport laundry firm has been fined after an employee fell through a mezzanine floor onto an industrial iron, sustaining third-degree burns.
The 34 year old man, a father of one, was in hospital for six weeks after the incident at Vineshield Professional Services Ltd in November 2013.
Trafford Magistrates’ Court heard (11 September) that an investigation by the Health and Safety Executive (HSE) found the company had failed to monitor the condition of the floor and did not ensure that it was of a suitable construction for the environment in which it was used.
Witnesses provided evidence to HSE that there were leaks in the roof which went onto the wooden floor and metal patches were found in several places where there were holes in the wood.
HSE inspector Helen Jones, speaking after the hearing, said:
“Vineshield Professional Services failed to carry out checks to ensure the floor was safe to work on. This was of importance due to the heat and steam generated in the working environment. An industrial iron giving off steam was situated directly underneath the mezzanine floor. The injured worker was severely burnt and had to undergo very painful treatment in hospital.”
Vineshield Professional Services Ltd, of Baxall Business Centre, Adswood Industrial Estate, Stockport, pleaded guilty to breaching Section 2(1) of the Health and Safety at Work Act 1974 and Regulation 12(1) of the Workplace (Health, Safety and Welfare) Regulations 1992. It was fined £20,000, plus £7,915.50 costs.
Notes to editors
- The Health and Safety Executive (HSE) is Britain’s national regulator for workplace health and safety. It aims to reduce work-related death, injury and ill health. It does so through research, information and advice, promoting training; new or revised regulations and codes of practice, and working with local authority partners by inspection, investigation and enforcement. www.hse.gov.uk[1]
- More about the legislation referred to in this case can be found at: www.legislation.gov.uk/
[2]
- HSE news releases are available at http://press.hse.gov.uk
Automotive components company fined
Automotive components company fined after worker injured
- Date:
- 10 September 2015
An automotive components company from West Midlands has been fined for safety failings after an employee suffered crush injuries after entering a guarded area of a machine.
Nuneaton Magistrates’ Court heard how on 30 September 2014 an employee of International Automotive Components Limited of Coleshill was maintaining a carpet forming machine. The employee had only been in the job for two weeks after being promoted from operator to tool changer.
While under supervision, the employee became trapped when the top hood of the carpet heating press descended on him while he was working.
International Automotive Components Company Limited, of Gorsey Lane, Coleshill, West Midlands was fined a total of £7,000, and ordered to pay £2,190 in costs after pleading guilty to an offence under Section 2(1) of the Health and Safety at Work etc. Act 1974.
Speaking after the hearing HSE Inspector John Glynn said: “It is no exaggeration to say the employee has been extremely fortunate to escape death in this incident.”
For more information about machinery safety log onto the website at
http://www.hse.gov.uk/toolbox/machinery/safety.htm[1]
Notes to Editors:
- The Health and Safety Executive (HSE) is Britain’s national regulator for workplace health and safety. It aims to reduce work-related death, injury and ill health. It does so through research, information and advice, promoting training; new or revised regulations and codes of practice, and working with local authority partners by inspection, investigation and enforcement. www.hse.gov.uk[2]
- More about the legislation referred to in this case can be found at: www.legislation.gov.uk/
[3]
- HSE news releases are available at http://press.hse.gov.uk
Safer Lorry Scheme
Safer Lorry Scheme
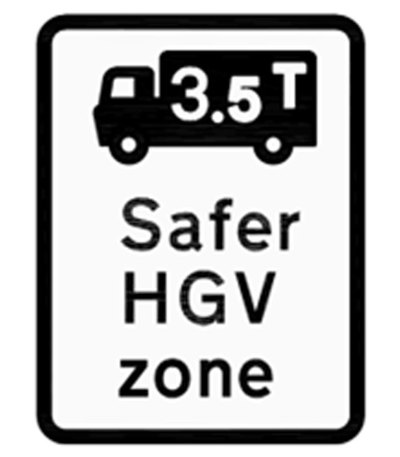
This new scheme uses a combination of powers held by these bodies to deliver a simple, quick and complete solution across all roads in London.
The scheme ensures that only lorries with basic safety equipment fitted will be allowed on London’s roads. Under London’s scheme, most vehicles that are currently exempt from national legislation for basic safety equipment will have to be retrofitted. This includes construction vehicles, which are involved in a disproportionate number of fatal collisions involving cyclists and pedestrians.
Under the scheme, vehicles over 3.5 tonnes that are currently exempt will be required to:
- Be fitted with Class V and Class VI mirrors giving the driver a better view of cyclists and pedestrians around their vehicles
- Be fitted with side guards to protect cyclists from being dragged under the wheels in the event of a collision
The scheme will operate across London, 24 hours a day, seven days a week, covering the same area as the Low Emission Zone (see a map of this area). It will come into force on 1 September 2015.
The scheme will be enforced by the Metropolitan Police Service, City of London Police and the Driver and Vehicle Standards Agency.
- Drivers found to be in charge of a non-compliant vehicle may be issued with a £50 Fixed Penalty Notice
- The offence also carries a potential fine of £1000 at Magistrate’s court
- The Traffic Commissioner, who has the power to modify or suspend operator licenses, will also be notified of companies operating vehicles in breach of the scheme
Global Energy Firm fined
Global Energy Firm fined £1.4m after worker killed in refinery fire
- Date:
- 29 July 2015
Total UK Limited have been fined £1.4 million after a major fire led to the death of a worker at an oil refinery in North Lincolnshire.
Twenty-four year old Robert Greenacre from Grimsby was working near a crude oil distillation unit just before the fire broke out at the Lindsey Oil Refinery (TLOR) in Immingham on 29th June 2010.
The Health and Safety Executive prosecuted the oil giant after an investigation found a fire was caused by an uncontrolled release of crude oil.
Hull Crown Court heard today (29 July) that Mr Greenacre who was a contracted fitter was working with a colleague beneath a distillation column containing hot crude oil. The job required them to open equipment beneath the column. When an item of equipment was opened, the crude oil was released. A short time later it ignited. Mr Greenacre’s colleague was able to escape the scene suffering minor burns, Robert did not escape and died beneath the column.
The court also heard operators of major accident hazard establishments must have in place a functioning system of risk assessment for all tasks where hazardous substances could be released.
Operators should always try to eliminate risk through hazard avoidance. In many circumstances this could be achieved by carrying out the task during shut-down conditions. Where this is not practicable, the highest achievable levels of isolation to industry standards are required.
Total UK Limited of One Euston Square, 40 Melton Street, London, pleaded guilty to breaching Regulation 4 of the Control of Major Accident Hazards Regulations 1999 (COMAH) and were fined £1.4 million and ordered to pay costs £34,084.05
Speaking following sentencing, Mr Greenacre’s family said:
“Despite the outcome of this case, it doesn’t change how we have been affected. Rob was our world. We have been left with a shattered and empty future, we are heart broken and changed forever”
Speaking after the hearing HSE Inspector John Moran said:
“If Total had followed well established principles of risk assessment this major fire and the subsequent fatal injury to Robert Greenacre could have been easily prevented.
“Although the accident arose from a simple task, the magnitude of the risk was great. The risk should have been identified before the task started, and action taken to either eliminate or control it. This did not happen.
“Total UK Limited as operator in control of a major accident hazard establishment fell far short of the standard required of them.
“This tragic incident should serve as a reminder to all such operators that if they fail to assess the risks associated with even simple and routine maintenance tasks, the consequences can be severe, and irreparable to the people involved and their families”
More information on COMAH can be found here: http://www.hse.gov.uk/comah/
Notes to Editors
- The Health and Safety Executive is Britain’s national regulator for workplace health and safety. It aims to prevent death, injury and ill health. It does so through research, information and advice, promoting training, new or revised regulations and codes of practice, and working with local authority partners by inspection, investigation and enforcement. www.hse.gov.uk
- Footage from the scene filmed by Humberside Police Helicopter Support Unit can be found here: https://www.youtube.com/watch?v=Ndk1qSxDycc
Scaffolding Unsafe Operation
Extendable Scaffolding Loading Bay Gate – use of cable ties to secure loose mesh and unsafe means of operation
Health and Safety Executive – Safety Alert | |
---|---|
Department Name: | Construction Sector |
Bulletin No: | FOD 2-2015 |
Issue Date: | 21 July 2014 |
Target Audience: | Construction industry; scaffolding companies; scaffolding suppliers; scaffolding manufacturers |
Key Issues: | Poor design of scaffold loading bay gate, providing inadequate edge protection to prevent falls from height. |
Introduction:
HSE has become aware that a number of manufacturers/suppliers are marketing an extendable scaffold loading bay gate that does not satisfy legal requirements or applicable standards when in some configurations. When extended the loading bay gate, which forms part of the edge protection on a scaffold, is not robust enough to fulfil this function and is therefore not suitable and sufficient to comply with the Work at Height Regulations 2005. This safety notice applies to all similar types of loading bay gate as described below.
Background:
The loading bay gates subject to this safety notice originate from a variety of manufacturers/suppliers and comprise two panels made up of tube and mesh (see photo 1). One panel section is fixed length and the other is telescopic and can be adjusted to the required width of the loading bay. This allows a width adjustment from approximately 2300mm to approximately 3900mm. The mesh infill spans the full width and height of each panel. There is no horizontal mid rail. This loading bay gate design is reported to be available in steel and in aluminium.
The mesh infill is typically 3 mm gauge on a 50 mm square pattern and each edge is welded to the fixed length panel. To allow the telescopic panel to slide during adjustment the mesh on this section is loose. Supplier instructions seen suggest the loose mesh should be fixed to the gate perimeter using plastic cable ties after this panel has been telescoped to a width suitable for the loading bay.
This type of gate has been found on a number of construction sites where the mesh was loose and able to detach when pushed (see photo 2) so would not be able to resist a person leaning or in particular falling against it, and would also allow loose materials to fall from the platform.
The gates in question open by rotating upwards around a pivot fitting mounted approximately 500mm inboard of the gate (see photo 3). Because this type of gate has very short rear levers it is usually opened by lifting the handles on top of the gate, placing a worker right at the edge of the platform with a gap beneath the gate that can exceed 1.5 metres high. When fully open there is a gap beneath the gate of approximately 1 metre height although this is about 1 metre inboard of the open edge of the loading bay (see photo 3).
The Work at Height Regulations 2005 Schedule 2 requires edge protection used for construction purposes to be of suitable strength and rigidity and to comprise the equivalent of a top rail, a mid-rail and a toe board. Where no mid rail is present any mesh panels or similar must be able to achieve an equivalent level of containment.
This safety alert does not apply to designs of upward rotating loading bay gate that are robust and are operated from the rear of the loading bay and which close off access to the loading bay when the gate is open. These should already comply with BS EN 12811-1:2003 ‘Scaffolds – Performance requirements and general design’ which sets out the standards expected for loading bay gates.
Action required:
- For gates of the type described in this safety alert stainless steel cable ties will be accepted as an interim measure for securing the mesh panel, and should be installed to the gate supplier’s instructions. Typically this will be one cable tie per 300mm. Unless the gate manufacturer/supplier allows a lighter duty cable tie, ties rated at minimum 75kg loop tensile strength should be used. Note that most cable ties are not designed to be suitable for reuse following loosening or removal. Alternatively, this aspect of the safety alert can be complied with by installing the extendible gate in the fully closed (narrowest) configuration thereby not requiring the use of cable ties.
- Stainless steel cable ties should be included as part of the 7 day scaffold inspection.
- Options to allow the gates in question to be opened without workers being able to slip or trip and fall through the gap underneath the open gate or the large gap while opening the gate include remote opening using rope over a scaffold rail or pulley fixed above and inboard of the closed gate. Or moving the gate pivot further inboard and extending the operating levers – this may remove the need to fully rotate the gate during opening. Both these methods allow operation from the rear of the loading bay platform – ie at least 2m back from the open edge.
- HSE has been informed that the supplier of one model of the gates in question is working on a design change to bring the gate to a standard that meets EN 12811-1 during operation and use. HSE expects manufacturers/suppliers of similar gates to do the same. These improvements will need to address the securing of the mesh infill panels; the risk of the gate opening due to a person or materials falling against it; and the level of fall protection provided when the gate is operated or open.
- Cable ties are not a permanent solution, However it is appreciated that many of these gates are manufactured and shipped from overseas and that changes will take time to implement. HSE will accept the correct use of stainless steel cable ties as an interim measure until the end of December 2016. After that date Enforcement Notices will be considered on a case by case basis for inadequate gates and/or gate designs. During the interim period gate installations that do not meet the minimum standard set out in this document will be subject to appropriate enforcement action.
Relevant legal documents:
The Work at Height Regulations 2005 – Regulations 8a, 10 and Schedule 2
References:
BS EN 12811-1:2003 Temporary works equipment- Part 1: Scaffolds – Performance requirements and general design
NASC Safety Guidance SG 4:10 Preventing falls in scaffolding
Safety Guidance SG 33:14 Guide to the construction and use of scaffold loading bays and loadbearing platforms.
Technical Guidance TG 20:13 A comprehensive guide to good practice for tube and fitting scaffolding. Operational Guide. Design Guide
Note: the NASC is currently reviewing its guidance in relation to loading bay gates and preventing falls in scaffolding.
The Scaffolding Association has stated that it intends to produce guidance on loading bay gates.
Further information:
Health and; Safety Executive,
FOD CD Construction Policy and Sector Unit
Rose Court
2 Southwark Bridge
SE1 9HS
General note:
Please pass this information to a colleague who may have this Product/ Equipment or operate this type of system/process.